by Julie | May 16, 2012 | Employee Training
One of the most common slurry tests performed for investment casting slurries is SiO2 percentage. Insufficient concentration of SiO2 in the slurry creates a weak shell. However, having too high a concentration can also cause a weak shell while potentially gelling the slurry.
The two common methods for measuring binder solids are volumetric and through the use of a densitometer. For this discussion, we will focus on the volumetric method.
Ensure that the sample has been spun long enough to remove the refractory particles from the supernate (liquid on the top of the solids). If this isn’t done, the results will be inaccurate, regardless of the test method utilized.
Of the two methods, the volumetric procedure can lead to the most variability. This variability can come from the following:
1. Uncalibrated flasks
2. Dirty flasks
3. Fill line identification
Most foundries make the mistake of assuming that a 10 ml volumetric flask filled with water will weigh10 grams. Making this assumption could lead to inaccurate results. However, if you compound this error with a dirty flask and the results will be even further off. I have seen the percentage of silica be off by up to 3 percentage points by not calibrating a dirty flask.
The other challenge that operators sometimes face is knowing how to locate the meniscus. By going through the calibration process, this can help operators understand how a slight difference in the fill line can impact the results.
The ICI has outlined a procedure on how to calibrate your flasks every time the test is performed. Or, if you have questions, feel free to contact me for more information at Julie@keyprocessinnovations.com.
by Julie | May 7, 2012 | Employee Training
I had a wise customer comment to me once that he didn’t mind collecting data as long as the operators/engineers were going use it for slurry control. I completely agree with that statement but would add: make sure the data you are gathering is meaningful.
So, what does meaningful data look like? In my mind, it would be data that you could rely on to troubleshoot issues within your process. One of my favorite examples was a customer who was measuring the pH of a slurry but his pH probe would never stabilize prior to turning off. Instead of resolving the issue, he would record the last reading he saw before the meter shut off.
Then, his slurry gelled – all 250 gallons. In the tank.
So, I received the panicked call that his slurry had gone bad and he didn’t know why.
When I asked about the pH of the slurry and if it had been trending down, he said he didn’t know. I asked if he had been testing for bacteria and he said yes, but was out of biocide. I asked if he had been checking conductivity levels and he said no.
Though he did a great job recording his data and graphing it for all to see, his data wasn’t accurate and he couldn’t use it for its intended purpose. It was an expensive lesson for the engineer and the company.
Collecting data for the sake of compiling a graph does not help you achieve the ultimate business goal of making castings. And, if you don’t have any confidence in the testing method, the technician or the result, than you might consider utilizing your resources in another capacity.
In the next few weeks, we will discuss ways to ensure you have robust slurry testing procedures.
by Julie | May 1, 2012 | Uncategorized
Last week, we discussed conductivity and how high levels can contribute to reduced slurry health. Now, we will discuss potential causes and what can be done about it.
Some common causes of high conductivity are:
♣ Increase in the number and strength of ions
♣ Bacteria
♣ Additions to the slurry
Most colloidal silica used in this industry is sodium stabilized. Sodium has a lower ionic strength than Iron, Calcium or Aluminum. As the concentration of ions increases in the slurry, especially higher strength ions, conductivity will increase.
One source of these higher strength ions is refractory flours. Some refractories have a high level of impurities that will leach out into the slurry. When this happens, the conductivity will rise and the pH will fall. The lower the slurry turnover rate, the greater the risk for slurry instability.
One way to remove these impurities is through the use of a rare earth magnet. There are a number of ways to install these magnets but, whichever method you choose, make sure they are easily accessible for cleaning. If you don’t clean the magnet on a regular basis, you will not reap the benefits. Start by checking it daily. As the build-up on the magnet decreases, the cleaning frequency can be reduced.
The presence of microbiological activity can also cause slurry conductivity to rise and pH to fall. If you experience this phenomenon, check for bacteria. If detected, treat with biocide, ammonium hydroxide or bleach.
However, using bleach to treat bacteria can have some other consequences including increased slurry conductivity, oxidation of polymers and reduction in shell hot strength. Do some investigation to identify the root cause of the bacteria. And then establish a regimen for preventing growth of bacteria in the slurries.
The unfortunate truth is there is no direct way to adjust conductivity, so it is important to take the appropriate steps to prevent slurry conductivity from climbing in the first place. But by following the tips above, you have the necessary tools to maintain conductivity levels in the optimal range.
by Julie | Apr 23, 2012 | Uncategorized
“How do I know when my slurry is going bad?” I have heard that question many times and I imagine standing over the slurry tank admonishing it by saying, “Bad Slurry! Bad Slurry!” But, let’s put humor aside, take a step back and understand the parameters that impact slurry stability. Most people understand that low pH is an indication of compromised slurry health. But, conductivity is frequently overlooked as another important indicator.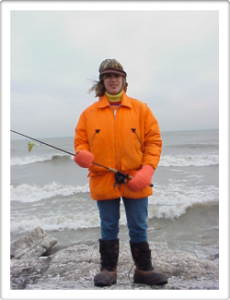
Conductivity is a numerical expression of the ability of an aqueous solution to carry an electric current. This depends on a number of factors including the presence of ions, total concentration and temperature.
In slurries using colloidal silica, the conductivity value reflects the ionic charge across the microscopic amorphous particles of silica dispersed in the aqueous solution. Let me try to explain it in slightly simpler terms.
An aqueous solution means that water is the solvent. As a reminder, water is made up of Hydrogen ions (H+) and Hydroxide ions (OH−). Colloidal silica particles are spheres of silicon dioxide (SiO2)with a negative surface charge (SiOH−). The water ions (H+ and OH−) form an electric double layer that results in a neutral charge surrounding the silicon dioxide molecules.
As the concentration of ions increase, i.e. conductivity increases, there is less space between the ions and the double layer begins to collapse and the silica particles are forced together forming the following permanent bond:
SiO2 – Si – O – Si – SiO2 + H2O
This reaction is what forms the gel network that holds the molds together when molten metal is poured into the shell. However, we want this reaction to take place during the shell building process, not in the slurry tank. If this reaction is occurring in the slurry tank, shell strength may be reduced.
Each colloidal silica has an optimal conductivity range so check with your supplier for specific information.
Now that you have a basic understanding of conductivity, next week we will discuss parameters that impact conductivity and how to address those issues.
by Julie | Apr 16, 2012 | Process Control
If your slurry control charts look more like shark teeth than an Iowa cornfield, perhaps you have some opportunity to control your process better. If you don’t have slurry control charts, do you know what is happening in your slurry over time? Charting your key parameters provides a visual indication of variability in your process. The easiest way to reduce variability is to control what is being added to the slurry.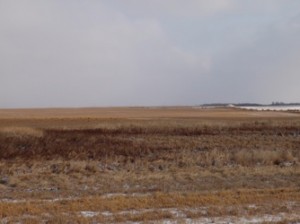
By spending some time reviewing slurry additions, you can minimize variability of key parameters during the shell building process. Here are a few tips to consider:
- SiO2 will climb over time so, have your target SiO2 for your make-up slurry about 1 to 2 percentage points below the center point of the dip tank range.
- Viscosity will also climb, so, target the make-up tank to be about 2 seconds below the dip tank.
- If pre-wet is being used, target a higher viscosity for the make-up tank. Do some experimentation to determine the optimal viscosity range of the make-up slurry to maintain the dip tank viscosity through slurry additions. The goal is to avoid making flour additions directly into the dip tank.
- Make sure that the pre-wet is being monitored and controlled for key metrics including SiO2, % polymer and bacteria.
- Educate your operators on when they should use water, binder or a binder-polymer “cocktail” when adjusting viscosity of both the make-up slurry and the dip tank.
- Monitor and control the make-up slurry as closely as the dip tank. Optimize the make-up slurry formulation so adjustments to the dip tank are minimal.
Steven Covey might not be an expert on precision investment casting, but he was correct when he said, “Begin with the End in Mind. ” Following these few simple steps will go a long way towards minimizing process variability while saving time and money.