by Julie | Sep 1, 2016 | Employee Training, Management, Safety
It is back to school time. I remember when I was younger, I was thinking about what to wear for the first day of school, making sure I had the perfect outfit for the school yearbook. But, as I got older, my focus turned to the subjects that I was going to be studying. Some my questions were: How hard is the professor? How much homework will she give us? How many exams will we have to take? As I reflect back, I don’t remember thinking much beyond passing each course. In fact, in Linear Analysis, a 400-level math course, the professor actually said and I quote, “I know I have a lot of engineering students in this class and you are wondering what the practical application is for this subject and I will tell you – I have no idea.” And he was right – I have never used anything I learned in that class in the real world.
But, as we look at training our operators, it is important that the information that is being presented has a practical application that the operators can apply to their work and/or personal lives. This doesn’t just apply to the training around their daily tasks, but, it also applies to safety training, HR training and environmental training.
When presenting training to operators, try to tie in real world experiences to the material. In the past, when conducting ladder safety training – I talked about how I almost fell off a ladder while cleaning my gutters at my house. Or when discussing PPE, I talk about the importance of wearing safety glasses, even when working on projects at your home. When discussing environmental training, I include tips on how to dispose of hazardous household chemicals.
If the training material is something that the operator can personalize and understand why it is important, at work or in his personal life, the training will have a much greater impact.
And if you do that, I am sure your operators will be more engaged and receptive than I was in Linear Analysis.
For more practical tips for manufacturing professionals to attract, train and retain your hourly workforce, go to www.keyprocessinnovations.com.
by Julie | Apr 28, 2016 | Consulting, Efficiency, Employee Training, Interim Management, Management, Safety
TRAINING WITHIN INDUSTRY
Over the past few years, I have had the pleasure of being an instructor at the Investment Casting Institute’s Process Control Class. It was in this class that I had my first introduction to Training Within Industry.
During World War II, there was a shortage of skilled and trained workers at a time when the demand on manufacturing was very high. As a result, Training Within Industry was developed to quickly and efficiently train operators.
There are four programs of Training Within Industry:
- Job Instruction (JI) – this component teaches trainers how to train
- Job Methods (JM) – a methodology that employees use to make their job easier
- Job Relations (JR) – an analytical method for addressing personnel issues
- Program Development (PD) –how to solve production problems that are unique to a particular organization
Each of the programs are broken into four steps and the training and implementation of these programs is very structured. However, the organizations which followed this approach realized unbelievable results. After the war, TWI became less common place in the United States, however, the Japanese learned about it and TWI is credited to be the foundation of Lean Manufacturing.
In the book Training Within Industry by Donald Dinero, the author states that “TWI helped lay the bases for “learning organizations,” where successful companies train their employees to question, think and solve problems. “
Can you imagine a better workforce than one that can question, think and solve problems? There are a number of resources available online to learn more about Training Within Industry. In the upcoming articles, I’ll provide more information on each of the programs.
For more practical tips for manufacturing professionals to attract, train and retain your hourly workforce, go to www.keyprocessinnovations.com.
by Julie | Apr 14, 2016 | Consulting, Employee Training, Interim Management, Management, Onboarding, Safety
THE START OF SOMETHING BEAUTIFUL
Starting a new job can be a little stressful. Meeting new people, learning new tasks and an adjusting to a new workplace culture. Can you think back to your first day with your current employer? Were you nervous? Excited? How were you greeted by your new peers? Was everyone expecting you?
Some employers seem burned out from the hiring phase – it is like a revolving door for new employees. Employees are hired and then they leave within a week or two resulting in more time and money spent on recruiting and training.
Without a doubt, hiring employees has gotten much more difficult in recent years. There is a shortage of skilled workers who have the workplace competencies needed in manufacturing. So, recruiting qualified candidates is much more difficult. (Check out this article on tips on recruiting the most qualified employees.)
But, once you have selected a qualified employee, you want to make them feel welcome. Have you thought about the first impression you give your new employee on their first day? Could you do more to let your new employees know you view them as a valuable member of your team? Here are few suggestions that could help in retaining your new employees:
- Interview current employees about what they thought about their first day, week or month with the company. What was their impression of how they were welcomed by the company? What is one thing they would like to see improved or implemented?
- Establish a mentor program so veteran employees can assist new hires assimilate into the culture.
- Create an employee based committee to assist in developing and instituting the onboarding process. You might even consider allowing them to participate in interviewing candidates.
- Provide a checklist for the hiring manager or supervisor so they can ensure the company is prepared for a new employee prior to the first day.
Establishing an onboarding program is an important part of retaining your work force (check out this blog for more information on onboarding). But, don’t overlook the importance of making a good impression on the first day. Making the employee feel welcome and helping them adjust to your culture can help retain a valuable new employee.
For more practical tips for manufacturing professionals to attract, train and retain your hourly workforce, go to www.keyprocessinnovations.com.
by Julie | Apr 7, 2016 | Consulting, Employee Training, Interim Management, Management, Onboarding, Safety
The goal in manufacturing is to SAFELY make an end product that meets customer specifications with the lowest cost possible. There is nothing more important than the safety of the employees. But even looking beyond the employee, having a strong safety culture also impacts your bottom line.
I recently met with a manufacturing professional who shared if you want to know if a company is profitable, ask them about their safety statistics. If they don’t know them off the top of their head or can’t find them quickly, they are probably struggling financially. Without a strong safety program, eventually the number of workplace accidents will start to climb.
When thinking about workplace accidents, I imagine an iceberg with 20% above the water and 80% below the water. The cost of the accident is the part above the water including doctor/hospital bills, employee time-off, etc. But, the actual cost is what is under the water which includes increased insurance premiums, higher payroll and reduced plant productivity.
But, you don’t have to take my word for it. I found a lot of data that supports the relationship between a strong safety culture and profitability, including the following:
- A Liberty Mutual survey reports 61% of executives say $3 or more is saved for each $1 invested in work place safety (http://www.the-osha-advisor.com/CASE.html)
- Participation in OSHA’s Voluntary Protection Program saved one company $930,000 per year and the company had 450 fewer lost-time injuries than its industry average (http://www.asse.org/bosc-article-6/)
- According to the American Society of Safety Engineers, investment in health and safety programs can result in saving in workman’s comp claims, liability damages and litigation costs in addition to improvement in productivity and employee morale.
Providing a safe workplace for your employees is a win-win. It is good for the employees and good for your bottom line. If you believe your safety program needs a little work, there are a number of resources available online including an article I recently wrote on the importance of reporting near-misses.
For more practical tips for manufacturing professionals to attract, train and retain your hourly workforce, go to www.keyprocessinnovations.com.
by Julie | Dec 23, 2015 | Employee Training, Safety
Over the past few weeks, the Pacific Northwest has experienced a deluge of rain, even setting some records for daily rain fall and consecutive days with measurable rain. As you can imagine, the traffic has been dreadful with landslides, flooding and lots of standing water on the roads. As I was trying to make it to an appointment last week, I started to think about some of the near misses I have experienced driving in the rain and I used extra caution to make sure I was prepared for those situations.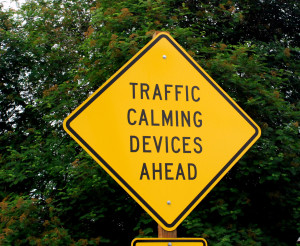
Being aware of near misses is an important part of building a safety culture. Did you know that for every accident, there are upwards of 30 near misses? And research shows that if you identify and address those near misses, the number of accidents can be reduced.
So, here are some tips on how to address those near misses:
- Have each employee report a near miss at some specified frequency, maybe every week or every month. The reporting near misses will increase the employees awareness of looking for unsafe practices or situations.
- Offer incentives for employees who report near misses.
- Treat every near miss as you would an accident. That includes investigation, determination of root cause and implementation of appropriate controls.
- Share near misses and lessons learned with employees.
As you move into 2016, perhaps this is the year to implement some changes to your safety program. And what could be a better gift to your employees than the gift of safety?