by Julie | Jul 14, 2016 | Efficiency, Employee Training, Management, Process Improvement
GETTING THE MOST OUT OF YOUR TECHNOLOGICAL IMPROVEMENTS
A member of my family recently purchased a new car with all the bells and whistles. This car came with a navigation system, internet access, adaptive cruise control and forward collision warning. Learning all the technology was overwhelming. But, what my family member forgot was that the primary purpose of the vehicle was to drive him from Point A to Point B. As you can imagine there were a few near misses as he learned how to handle all the technology right at his fingertips.
Learning new systems or technology can be challenging, especially if the person isn’t particularly tech savvy. As the individual focuses on learning the newly installed systems, he may lose focus on other important tasks such as safety or product quality. Understanding and planning for this loss of focus is important as new technology is introduced to your operators. This may require a reduction of throughput during the initial learning curve or possibly staffing additional operators so throughput and/or quality aren’t compromised.
As you develop your training plan, make sure to incorporate as many senses as possible including auditory, visual and kinesthetic. Everyone learns a little differently and incorporating different senses can increase the speed at which an operator learns the necessary information. Never don’t underestimate the importance of hands-on learning.
When you train your employees on the new systems, keep an eye out for the operators who appear to be struggling. If you are picking up on it, then their peers probably are as well and this can result in anxiety and a reduction of focus by the struggling employee(s). Consider some contingency plans for these employees where they can get additional training without being scrutinized by their peers.
Technology can be an asset to a manufacturing plant, but, make sure that you incorporate the necessary operator training systems so you can realize all the benefits without a negative impact to operator safety or product quality.
For more practical tips for manufacturing professionals to attract, train and retain your hourly workforce, go to www.keyprocessinnovations.com.
by Julie | Jul 6, 2016 | Efficiency, Employee Training, Management, Process Improvement
Understanding Your Operators Resistance to Change
How many times have you heard the phrase, “I’ve been doing this for over 20 years and this hasn’t been an issue before” Or “What makes you think we need to change this now?” I think those phrases are code words that could touch on some underlying issues including:
- Fear of change. This fear can be twofold: what I have been doing all these years has been wrong so now I have to change or what I thought was secure is now changing leading potentially to some period of uncertainty. Preparing employees for change can help them overcome this fear. I have conducted change management seminars to help management teams adjust to shifts in the workplace. But, I also know that change gets easier the more it is experienced. So, if you are sensing resistance from your team, you might want to make some small changes which can help your operators adapt to an ever-changing work place. Or, if a large change is planned, take the time to train your operators on why change is necessary along with suggestions on how to manage the stress of change.
- Mistrust. Most long-term employees have been doing the same thing for many years and now, you are asking them to change. Questions I have heard include: Why do you all of sudden think that I need to make a change?What is your motivation for making me change? Are you are trying to make yourself look good and me look bad? Operators, especially long timers, are observant. If they sense that management isn’t being honest with them, they will fight the changes that are being implemented. An attitude of open, honest and consistent communication will go a long way towards overcoming mistrust.
- Prejudice. After a certain amount of time, adults will develop an attitude towards an individual or group of individuals which will frame their thinking. These prejudices can impact an adult’s willingness to adopt new ideas. As a young engineer, I heard over and over again, typically in a sarcastic tone, “Oh, the engineer is here to tell us what we are doing wrong.” In order to overcome these prejudices, I spent time listening to the operators, asking for their input and implementing some of their ideas. Yes, it took time, but, eventually, I found these operators much more willing to work with me. However, these prejudices won’t go away overnight and require a willingness from all parties to work together and make sure each side is being heard and understood.
As you approach training of your workforce, it is important to keep these potential issues in mind. Put yourself in your employee’s place and think about the best approach to introducing new methods and concepts. The more time that is spent developing the training and addressing some of the underlying concerns, the greater the impact the training can have on your workforce.
For more practical tips for manufacturing professionals to attract, train and retain your hourly workforce, go to www.keyprocessinnovations.com.
by Julie | Jun 29, 2016 | Efficiency, Employee Training, Management
TIPS TO KEEP MILLENNIALS ENGAGED IN THE WORKPLACE
I recently had an opportunity to serve as judge for a STEM (Science, Technology, Engineering and Mathematics) middle school project titled “The School of the Future.” The project was based on 4 criteria: the learning environment, the physical environment, community interaction and environmental impact. Some of the students had amazing ideas and designs while some of them didn’t seem to embrace the project. As I listened to over 30 presentations, I started to pick-up on some themes including:
- Students find value in project based learning. They reject the notion that they need to learn individually.
- They want to be in control of their curriculum
- Most of their research is done on Google
- They believe that learning should be fun
- Utilizing technology is important
- Protecting the environment is a priority for them
I’m not suggesting that I completely agree with them and there were times when I questioned their thought process. But, it was an interesting glimpse into how millennials think.
So, how does that impact us in the work place? This is a different generation and they aren’t going to think like we do. So, we need to adapt our approach so we can keep them engaged. Some suggestions on how to do this include:
- Consider providing opportunities for your employees to work together on a project, such as Kaizen events, department specific 5S or even utilizing process improvement tools such as Brainstorming/Cause and Effect Diagrams.
- Incorporate technology into your plant. This doesn’t need to be a complete overhaul of your plant. Some less expensive ways to use technology to engage your employees could be a company e-newsletter developed by your employees, or transition training into an interactive portal where they can establish their own curriculum and schedule (within reason, of course).
- When you do conduct live training, ensure it is interesting and engaging. If it isn’t, check out this article on ways to improve it.
- Identify a company sponsored project outside of the plant to help millennials feel engaged at work. Perhaps your company can get involved with Earth Day, or some other cause that resonates with your employees, industry and/or your community.
Millennials aren’t going to change and it is up to us to modify our approach so they can stay engaged at work. Because, if we don’t, they will find an employer who will adapt their approach to meet their needs.
For more practical tips for manufacturing professionals to attract, train and retain your hourly workforce, go to www.keyprocessinnovations.com.
by Julie | Jun 10, 2016 | Efficiency, Employee Training, Management, Process Improvement
BENEFITS FOR HAVING A CROSS-TRAINED WORKFORCE
If you are like me, you have summer on your mind. This is my favorite time of the year in the Northwest – the rain stops and the sun comes out. Long days, warm nights. And family vacation season!
Without good cross training, productivity of your plant may suffer when employees take their vacations. In order to avoid any negative impacts, some companies allow employees to skip their vacations and pay them for the week. That might seem like a tempting practice as it reduces the burden of having to cross train and increases the take home pay of the employee, but studies show that without taking time off, employees are more likely to make mistakes, increase health issues or burn themselves out.
A cross-trained workforce is the key to covering vacations as it provides the flexibility to move employees between departments. But, cross-training takes time. And since vacation season is upon us, I put together a list of other suggestions to help manage the vacation season so both the employee and the employer remain healthy:
- Have an up-to-date skills matrix. A skills matrix allows at a quick glance to see which positions are the most vulnerable. Using this matrix, you can approve vacation requests ensuring sufficient coverage for each position. For more information on how to establish a skills matrix, check out this article.
- Provide employees an opportunity for refresher training so they remember how to do a particular job before they are moved to fill in for a vacationing co-worker.
- Hire high school or college students on summer break. Manufacturing jobs are typically better paying jobs than fast food and it is a great way for them to get a taste for your company or industry.
- Consider an all plant shut-down. This has the advantage of not having to cover vacations and allows for annual maintenance. However, it doesn’t provide flexibility for the employee who may want to vacation outside of the shutdown window.
- Flex the work week. Perhaps moving to 4-10 hour days or staggering shift start times will give extra time for employees to enjoy with their families.
At the end of the summer, set up some time with your team to discuss what went well and what could be improved upon. And use the fall and winter to make improvements so next summer, you will be Having Fun in the Sun!
For more practical tips for manufacturing professionals to attract, train and retain your hourly workforce, go to www.keyprocessinnovations.com.
by Julie | May 17, 2016 | Consulting, Efficiency, Employee Training, Management
Training Supervisors on Conflict Resolution
Dealing with conflict is an important part of a healthy work environment. And making sure people have the skills to resolve those issues was so important that Job Relations Training was included as one of the four programs within Training Within Industry. Donald Dinero in his book “Training Within Industry” said Job Relations Training “gives supervisors an easy method to use on a daily basis to inform their decisions and make their jobs easier.”
The program includes a 4 step method for handling conflict. As I read through the 4 steps (Get the Facts, Weigh and Decide, Take Action and Check Results), I thought about how difficult it can be to take unemotional approach to a situation where you are emotionally involved.
But, being effective in a supervisory role requires the ability to look beyond the emotions and focus on what is best for the organization. The importance of a supervisor is often overlooked but, he or she probably has one of the most difficult positions within a manufacturing plant. It is the supervisor’s responsibility to produce consistent results in order to meet the business objectives, however, they are also responsible for addressing the day to day concerns of the hourly employees. I imagine the supervisor being pulled in both directions when at times, these two groups are perceived to be diametrically opposed. The supervisor is expected to be calm under pressure, patient, demanding, understanding, unyielding, etc.
Have you looked at the organization through the supervisor’s glasses? Do they have the skills they need in order to keep your organization moving in the direction you want it to move? Are they getting the support they need in order to address the concerns of the hourly work force while focusing on the organizational goals?
For more practical tips for manufacturing professionals to attract, train and retain your hourly workforce, go to www.keyprocessinnovations.com.
by Julie | May 5, 2016 | Consulting, Efficiency, Employee Training, Onboarding
Introducing Job Instruction Training
One way to remove variability from your process is to ensure the operators are properly trained. Sounds easy enough – but how do you go about doing that?
Fortunately, a proven methodology has already been developed. Job Instruction Training (JI), one of four programs contained in Training Within Industry (see this blog for more information on TWI) covers this important topic. According to JI, training can be broken down into the following steps:
- Prepare the Operator. People tend to be nervous before learning something new and this can impact the learning process. So, try to relax the operator while learning more about him, including any relevant experience. You also want to explain why what they are learning is important and how this task relates to the overall manufacturing process.
- Present the Operation. Explain each of the steps in the operation, identifying key points along with the reasons for each step. Describing each step while the operator watches will help the operator learn much faster. The more senses that are utilized during learning will increase the retention rate and speed.
- Perform the Operation. Once the operator has seen the steps performed and had the key points and reasons explained, now is the time to try it himself. As the operator works through the steps, have him explain the key points and reasons for each step. Be patient as the operator walks through each of the steps taking the time to check for understanding by asking questions.
- Follow-Up. Once you feel the operator has a good understanding of the process, you can leave him alone. But, make sure you check back with him periodically (more frequently initially) to ensure the steps are being followed and he doesn’t have any questions.
After reviewing this information, you probably had a similar reaction as me which was “this seems fairly straightforward.” However, I also wondered how many instructors have been taught how to train an employee to do a new job. Without a doubt, it is possible to be successful without a fully defined training methodology, but, I wonder, how much more efficient and effective could you be if you took the time to establish a formal training method for your instructors to follow?
For more practical tips for manufacturing professionals to attract, train and retain your hourly workforce, go to www.keyprocessinnovations.com.
by Julie | Apr 28, 2016 | Consulting, Efficiency, Employee Training, Interim Management, Management, Safety
TRAINING WITHIN INDUSTRY
Over the past few years, I have had the pleasure of being an instructor at the Investment Casting Institute’s Process Control Class. It was in this class that I had my first introduction to Training Within Industry.
During World War II, there was a shortage of skilled and trained workers at a time when the demand on manufacturing was very high. As a result, Training Within Industry was developed to quickly and efficiently train operators.
There are four programs of Training Within Industry:
- Job Instruction (JI) – this component teaches trainers how to train
- Job Methods (JM) – a methodology that employees use to make their job easier
- Job Relations (JR) – an analytical method for addressing personnel issues
- Program Development (PD) –how to solve production problems that are unique to a particular organization
Each of the programs are broken into four steps and the training and implementation of these programs is very structured. However, the organizations which followed this approach realized unbelievable results. After the war, TWI became less common place in the United States, however, the Japanese learned about it and TWI is credited to be the foundation of Lean Manufacturing.
In the book Training Within Industry by Donald Dinero, the author states that “TWI helped lay the bases for “learning organizations,” where successful companies train their employees to question, think and solve problems. “
Can you imagine a better workforce than one that can question, think and solve problems? There are a number of resources available online to learn more about Training Within Industry. In the upcoming articles, I’ll provide more information on each of the programs.
For more practical tips for manufacturing professionals to attract, train and retain your hourly workforce, go to www.keyprocessinnovations.com.
by Julie | Mar 31, 2016 | Consulting, Efficiency, Employee Training, Interim Management, Management
WITH RIGIDITY OR FLEXIBILITY?
One of the reasons operators are trained to do a task the same way is to ensure uniformity and reduce process variability. However, this approach may not take into account how operators should react to slight process variations.
Yes, we want consistency from operator to operator but, we also want the operator to be aware of process fluctuations and adjust accordingly. One of the benefits of having an operator do a job rather than a robot is that they can observe the process. However, operators need to know what to do when slight changes are observed. Should they modify the process or stop production and notify management?
Some argue that operators should all do the same thing and not make any changes to the process. Others suggest that it is best to have operators aware of the overall process and the desired end result and then give them the flexibility to modify the steps based on their perceived best method. I see benefits and challenges with each of those approaches.
If operators are instructed to follow the process exactly as they were trained, the following questions come to mind:
- What is the impetus for making improvements to the process?
- What if a shift in the process impacts the final product?
- How do the operators provide input for a better method?
- Who decides whether this new method should be implemented?
If the operators have the flexibility to modify the process based on their perceived best method, I start to question:
- How do the operators know that their modification won’t impact product quality?
- Is their modification the most ergonomic method?
- Will other operators try the same modification but achieve a different result?
Regardless of the how you approach improvements to a process, it is critical that the operators have input. They work in the process on an ongoing basis and will detect subtle changes that might otherwise go unnoticed. Establishing a method for incorporating process improvements will go a long way towards reducing process variability.
For more practical tips for manufacturing professionals to attract, train and retain your hourly workforce, go to www.keyprocessinnovations.com.
by Julie | Feb 25, 2016 | Consulting, Efficiency, Employee Training, Interim Management, Management
A lot of people claim to have a “6th Sense” when assessing a situation. But, when it comes to making a business investment, having a benchmark and being able to quantify improvements is essential. Making process improvements in your process may require an investment in financial, personnel or temporal resources and in order to justify the investment, you may need more than a sense in order to get the necessary support. 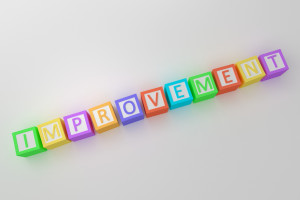
No matter what problem solving methodology used within your plant, most start by defining the problem. And part of this initial step includes identifying measures of process performance and establishing a baseline. An often overlooked reason for this step is to ensure the gains are sustained after improvements have been implemented.
Listed below are some metrics that can be used to measure process performance.
- First Pass Yield. This measures the number of good units produced against the total number of units produced. Depending on your process, this measurement can be broken down by department, by machine or by operator.
- Value Added vs Non-Value Added Time. Gathering data for this can be done via Value Stream Mapping or through Time Observations. From these studies, value and non-value added steps can be identified. As non-value added time is reduced, process output should increase.
- % Uptime. By defining % Uptime as outlined below, this measurement also takes into account set-up, changeovers, loading, unloading, idle time, breaks, cleaning, maintenance, etc.
% Uptime = (Value Added Time) x 100
(Operating Time)
- Process Capability, Cp or Cpk. In order for a process to be considered capable, it needs to be stable. Process stability means having consistent centering around the mean and predictable variation.
As you look towards making improvements in your process, try to pick a metric currently in use (or one that should be implemented) and use that to establish a baseline. Then utilize that metric to show areas which need improvement. Additionally after changes are made, data is available to document the improvement and provide a metric to sustain the gains.
For more practical tips for manufacturing professionals to attract, train and retain your hourly workforce, go to www.keyprocessinnovations.com.