by Julie | Dec 23, 2015 | Employee Training, Safety
Over the past few weeks, the Pacific Northwest has experienced a deluge of rain, even setting some records for daily rain fall and consecutive days with measurable rain. As you can imagine, the traffic has been dreadful with landslides, flooding and lots of standing water on the roads. As I was trying to make it to an appointment last week, I started to think about some of the near misses I have experienced driving in the rain and I used extra caution to make sure I was prepared for those situations.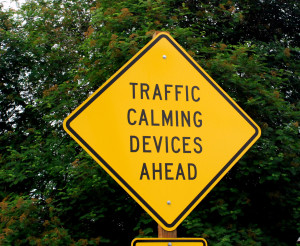
Being aware of near misses is an important part of building a safety culture. Did you know that for every accident, there are upwards of 30 near misses? And research shows that if you identify and address those near misses, the number of accidents can be reduced.
So, here are some tips on how to address those near misses:
- Have each employee report a near miss at some specified frequency, maybe every week or every month. The reporting near misses will increase the employees awareness of looking for unsafe practices or situations.
- Offer incentives for employees who report near misses.
- Treat every near miss as you would an accident. That includes investigation, determination of root cause and implementation of appropriate controls.
- Share near misses and lessons learned with employees.
As you move into 2016, perhaps this is the year to implement some changes to your safety program. And what could be a better gift to your employees than the gift of safety?
by Julie | Dec 3, 2015 | Consulting, Employee Training, Interim Management
Over the Thanksgiving holiday, my husband and I flew back to Wisconsin to be with family. Unfortunately, Chicago was experiencing its first big snow storm of the season and flights into the airport were being delayed. So, we sat in Portland waiting for our flight to take off. We kept hearing we would get flight updates in an hour, then the hour came and it was another flight update in 30 minutes. The airline handled the situation well and despite being a weather delay, they even handed out food vouchers as we waited.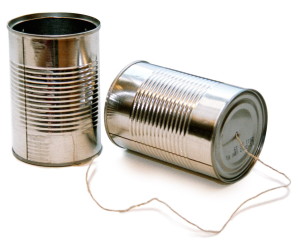
After four hours, Chicago Air Traffic Control lifted the ground stop and gave our flight a departure time. So, we all line up and started boarding the aircraft. In the middle of boarding, the crew told us to stop, gather our belongings and get off the plane. Apparently, the pilots had timed out and left the airport, leaving us with no one to fly the plane. So, we all de-planed feeling rather frustrated with the airline.
I heard one traveler ask the flight attendant why the ground crew had us start boarding when they didn’t have a pilot. Her response was that there was no communication between the ground crew and pilots only between the ground crew and the flight attendants.
As we waited for a pilot, I thought about how a simple process of communication between the pilots and ground crew could have avoided the frustration of having passengers deplane. And all the good will that the airline earned during the weather delay was erased due to poor internal communication.
As you look at your internal processes, do you see areas where enhanced communication could improve your customer experience? Could improved internal processes protect your customer’s good will that you try so hard to earn?
Looking for some ideas on how to improve your internal processes? Let’s talk – I know I can help!
by Julie | Nov 4, 2015 | Consulting, Efficiency, Employee Training, Interim Management
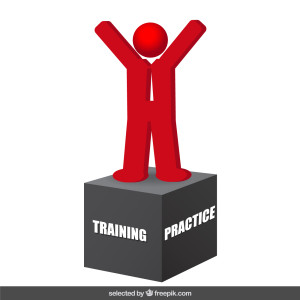
Business vector designed by Balasoiu – Freepik.com
As an athlete, I have some recurring injuries that flare up when training for an event. Since my issues were always on my left leg, I often joked that I should just cut off my left leg and grow back a new one, preferably without these nagging injuries.
While that might seem like a far-fetched idea, I had client who was having systemic issues with their workforce and made the decision to fire a majority of the employees and then hire new employees. In their mind, this would resolve the inherent cultural issues and allow them to hire operators with a skill set that would be better suited to support the new direction of the company.
What appeared to be overlooked was the amount of time required for an operator to master a specific job function. How would a new employee learn those skills if they weren’t taught by someone who possessed them? How long would it take to develop those skills?
Here is what I believe to be true about operators – they don’t purposely decide to do a bad job. People inherently want to take pride in their work. So, if they aren’t following the process, the logical question is why?
So, we started asking questions, including:
- Do the operators know and understand what is expected of them?
- Do the operators receive feedback on their individual performance and the performance of the department?
- Are there established procedures to follow?
- Have the operators been trained on the procedure(s)?
After reviewing the responses from the questions above, I proposed a different approach. Start by training the employees on what is expected of them and put the systems in place to ensure the training is reinforced. This isn’t as drastic as hiring all new employees, but, in the end, the results are much more sustainable.
So, just like my nagging sports injury, we identified the root cause of the problem and strengthened the areas that were causing issues. And over time, the organization became much stronger. Do you have some issues that are keeping your organization from operating at maximum efficiency? Let’s connect and see if we can work together to make your organization healthy and happy.
by Julie | Sep 9, 2015 | Consulting, Efficiency, Interim Management

During a recent assignment, I was the acting Interim Director of Manufacturing while an executive was putting a new management team in place. This was a difficult time for the company – scrap was at an all time high, a manager with almost 20 years of knowledge had just been let go and they had just failed a quality audit which put their business at risk with some of their customers.
During periods of transition, I have found it beneficial to give a team something to focus on. So, my mantra was simple: Safety, Quality, Communication. Safety of employees is always first and foremost. Quality must be a priority for every employee. And effective Communication is key to efficient operation of a business.
Changing the safety culture wasn’t easy. We started with personal protective equipment (PPE), specifically safety glasses. Once that was in place, we focused on slips, trips and falls, a top cause of safety related incidents. It took time but, slowly, the employees began to accept and embrace the changes.
We also focused in cleanliness of the plant. Cleaning up the plant went a long way towards improving the way the employees viewed not only their work area but also the quality of their work. Positive feedback on plant cleanliness from customers and vendors reinforced the habit.
Improving the quality of the parts we produced required educating the operators on their work and how it impacted the final product. While there was a quality system in place, the system hadn’t been fully embraced by the operators. Often times, operators didn’t understand how their individual job could impact part quality. The answer to the question, “Do you want good parts or parts at the specified rate” was Yes. And, if operators were struggling to make good parts, we took the time to fix the problem, not apply a band-aid.
Open communication was lacking with the previous manager. And it took time for the employees to change the way the spoke with each other. After a few coaching sessions, I overheard one of my direct reports say to another, “Our manor of communication needs to change.” And from that comment, I realized we were on our way.
Of course there were other obstacles that we needed to overcome. But slowly, we made improvements to the plant, scrap, and culture. Having a mantra that the employees could focus on during the period of change was vital to sustaining the business during the period of transition. Is your business in a period of transition? Do you have a mantra that your operators can focus on? If you need some assistance as you transform your business, emailme so we can arrange some time to talk. Together, we can make your business thrive.
by Julie | Jan 18, 2013 | Employee Training
How much time is spent thinking about slurry viscosity control? My guess is, not much. It seems to be a necessary evil of running a shell room, but not an area where we spend a lot of time.
What is the impact of the slurry viscosity being out of range? Operating outside of the targeted range could result in variations in shell thickness. If the back-up viscosity is running thick, then the mold weight could increase by up to 10%, especially in the later dips. If the viscosity is below the lower limit that could result in a thinner slurry layer and potential shell failures including run-outs or surface finish defects.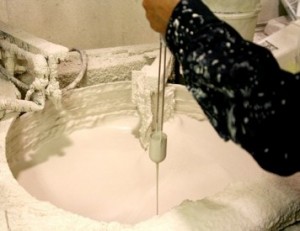
What is viscosity and why do we measure it? Viscosity is the measurement of a fluid’s resistance to flow, in our case, the slurry. A number of factors can impact the slurries viscosity, including liquid content (silica, water and polymer), particle size of the flour and temperature, to name a few.
Assuming a slurry is within specification for its key parameters, i.e. percent silica, temperature and refractory solids, the viscosity measurement is a value used in this industry which identifies how much slurry will be deposited on the wax pattern and/or previous dips. The ideal viscosity for slurry is dependent on the type of slurry and the part configuration. This is normally set by shell room management or by the supplier. The operator’s responsibility is to maintain the slurry within the designated range.
Viscosity is typically measured using a viscosity cup or in some instances a viscometer. Most commercial foundries using a viscosity cup establish a 2-second range and try to maintain the viscosity within that range.
However, the different techniques used by operators while measuring viscosity can have an impact on the value they record.
- To Rinse or not to Rinse: If the cup is stored in water, is it rinsed with slurry prior to taking a reading?
- Why Stop at One Reading: How many readings should be taken prior to recording?
- Location, Location, Location: Where in the tank is the slurry most uniform?
- Blink or ¼” stream: Are the operators looking for a blink or a stream break? If a stream break, what distance from the cup?
How you measure viscosity isn’t as important as ensuring that all your operators are doing it the same way. The amount of time it takes for a slurry to flow through a cup is relative, not absolute. But, you want your operators to minimize the variation.
Some operators are very comfortable taking viscosity readings. Inevitably, there will be an operator who is not comfortable measuring viscosity and his readings will be significantly different from the other operators. If the slurry is being adjusted based on this operator’s reading, the slurry could be adjusted to be out of the range.
Once you understand how viscosity control is being managed, you can start to address the variations. Training them not only on the viscosity procedure but also on why viscosity is important can go on long way towards improving viscosity control.
The final step is to continue to follow up on a regular basis to ensure that the operators are following the established procedure and reinforce the importance of viscosity control.